A cementgyári hulladékégetésről
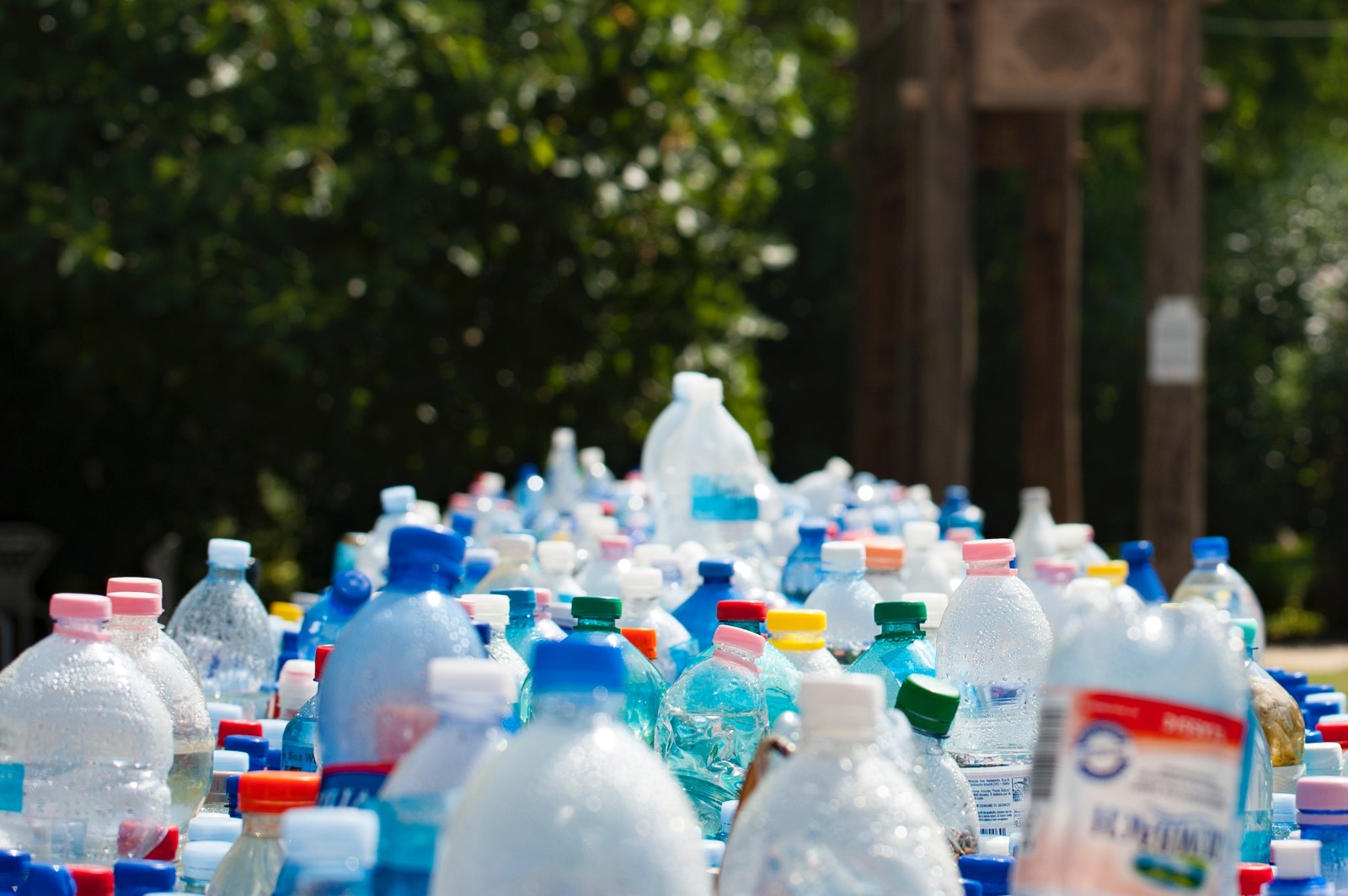
A hulladékgazdálkodási jogszabályok alapján a használt gumiabroncsot Magyarországon az EU tagországaihoz hasonlóan 2003 júliusától egészben, 2005-től pedig még darabokban is tilos lesz települési szilárdhulladék-lerakóban elhelyezni. Az eddigi szokástól eltérően tehát a végső lerakás helyett más módszerekhez kell folyamodnunk. Ha nem sikerült megelőznünk a hulladék képződését, akkor újrahasznosítással, illetve a lehető legkisebb környezetterhelést okozó égetéssel érdemes próbálkozni. Lássuk, milyen lehetőségek léteznek!
Az újrahasznosítás módszereinek kidolgozására több kísérlet is folyamatban van. Az egyik lehetőség a ledarált autógumi útalapba keverése, amelyre egyes nyugat-európai országokban több példát is találhatunk. A másik megoldás az anyagában történő újrahasznosítás az így előállítható termékek köre azonban korlátozott, hiszen biztonsági okokból új autógumit nem gyártanak a régiekből. Az egyik dél-dunántúli vállalkozástól nyugati cégek vásárolják meg az aprított gumihulladékot, és például mosógépek alá gyártanak belőle gumiszőnyeget. Az ilyen jellegű újrahasznosításkor azonban az abroncs acélrésze, vagyis az autógumi mintegy fele hulladékként megmarad, és továbbra is problémát okoz. A probléma kezelésének másik eszköze a hulladékégető-mű, amelyben kizárólag energianyerésre használják az abroncsokat, az égetési hőmérséklettől függően egészségre káros gázok kerülnek a légkörbe, s a folyamat végén veszélyes hulladék marad vissza.
A felvázolt kezelési módok köztes változatát képezik a cementgyárak, amelyekben a gumiabroncs nemcsak fűtőanyagként szolgál, hanem egyes részei a cementmátrixba beépülve adalékanyagot váltanak ki, ezáltal a szükséges fosszilis tüzelőanyagok mellett a nyersanyagok (adalékanyagok) mennyisége is csökken. A folyamat során a megfelelő technológia alkalmazása esetén nem kerül egészségkárosító anyag a levegőbe, s hulladékképződéssel sem kell számolni.
Ez utóbbi gumihulladék-kezelési lehetőség vizsgálata következik az alábbiakban, a dél-baranyai Beremend cementgyárának működő példáján keresztül.
Hazánk legdélebbi pontja közelében található a Duna-Dráva Cement Kft. Beremend Gyára. A cementgyártás alapanyagát, a mészkövet és az agyagot a római kor óta működő szársomlyói bányából (amelynek külső tájsebét a Duna-Dráva Nemzeti Park Igazgatósággal megegyezve már nem növelik tovább a hegy ugyanis igen ritka növény- és állatfajok élőhelye), és a jelenleg ennél jóval nagyobb kapacitással működő beremendi bányából szállítják. A tüzelőanyagok közül a pakura (nehézolaj) helyett fokozatosan a szénportüzelésre térnek át (a szén kéntartalmát a cement alapanyaga, a mészkő megköti, így a széntüzelés nem jelent nagyobb környezetterhelést), kiegészítésként földgázt használnak.
A gyártási folyamat során az alapanyag előkészítést (aprítás, őrlés, szárítás) követően a 2000 °C lánghőmérsékletű égő melegítette kemencébe kerül, s ott 900?1450 °C hőmérsékleten lép reakcióba az adalékanyagokkal, s képződik belőle cementklinker. Ebbe a fázisba kapcsolódik be a használt autógumi útja: a gyár gumiadagolója a nagy munkagépek abroncsainak kivételével minden típusú autógumit (személy- és tehergépkocsi, kamion stb.) képes fogadni. A kemencébe ejtés előtt a gumit lemérik, s tömege alapján számítják ki az elégéséhez szükséges időt, vagyis a következő abroncs sorra kerülésének időpontját. Óránként 960 kg gumihulladék kerül mindkét kemencébe. A hamarosan megépülő folyamatos emissziómérő rendszer üzembe helyezésével az engedélyezett mennyiség a jelenlegi 980 kg/óráról 20?25 százalékkal növelhető (az adagoló kapacitásának függvényében).
Az üzemnapló tanúsága szerint a kemencébe 990?1020 °C közötti hőfokon kerülő anyagok 5?6 másodpercig tartózkodnak 1200 °C feletti (nagyrészt 1450 °C) hőmérsékleten. Ez a hőmérsékleti tartomány és tartózkodási idő (valamint az égés és utóégés során rendelkezésre álló fölös oxigén) sokkal nagyobb biztonságot ad az égéstermékek szempontjából, mint a hulladékégető-művekre előírt, legalább 2 másodperces 850 °C feletti tartózkodás. A magas hőmérséklet (és az általa nyújtott biztonság) betartására garanciát nyújt az a tény, hogy 1420 °C alatti hőmérsékleten nem alakul ki a cementklinker.
Az égetés során képződő savas gázokat (kén-dioxid és hidrogén-klorid) a nagy mennyiségű aktív mésztartalom semlegesíti, és az előforduló nehézfémek (vas, króm, kobalt, réz, titán, mangán, molibdén, vanádium, cink) is megkötődnek, beépülnek a cementbe, s annak felhasználását követően a betonból sem oldódnak ki. Melléktermékek (égési maradék, gáztisztításból származó pernye stb.) nem képződnek, mert ezeket visszaforgatják a gyártási folyamatba, s szintén beépülnek a cementbe.
A beremendi gumiégetés története két szakaszból áll. 1984 és 1991 között már végeztek ilyen tevékenységet, azonban az állami támogatás hiánya és a járulékos költségek (a többi tüzelőanyagtól elkülönített adagolórendszer, rakodás stb.) miatt nem volt kifizetődő. 1997 óta a termékdíjból származó állami támogatásnak (jelenleg 11 Ft/kg) köszönhetően rentábilisan üzemeltethető a rendszer.
A kemencénkénti 960 kg/óra elégetett mennyiség éves szinten mintegy 11000 tonna gumihulladék kezelését jelenti, ami a hazai éves kibocsátásnak körülbelül egynegyede, s szinte az egész Dunántúl gumihulladékát érinti. A gyár évente egymillió tonna cementet állít elő. Az eddigi működés 12 éve alatt 106 ezer tonna autógumit égettek el, amelynek begyűjtését a pécsi székhelyű Biokom Környezetgazdálkodási Kft., mint rendszergazda végzi. Jelenleg 9 százalék a gumi részaránya a tüzelőanyagban.
Egyéb másodnyersanyagok felhasználása: A tüzelőanyagként alkalmazott gumiabroncsok mellett ? cement kiegészítő adalékanyagként ? egyéb másodlagos anyagokat is felhasználnak a beremendi cementgyárban. A pécsi hőerőmű elektrofiltereiről érkező pernye, a dunaújvárosi kohósalak, a piritpörk és a visontai erőmű füstgáz-kéntelenítőjében keletkező anyag (az ún. REA gipsz) itt biztonságosan felhasználható ? ezáltal kevesebb zagytér és salakhányó éktelenkedik az országban, sőt természetes anyagokat váltanak ki a cementgyártás során.
Az emisszió rendszeres ellenőrzései kimutatták, hogy a gyár kéményén gumi együttégetés esetén is ugyanazok a gázok (a magas égetési hőmérséklet miatt főként nitrogén-oxidok) és por, ugyanolyan mennyiségben távoznak, mint anélkül. A szilárd alkotóelemek ugyanis beépülnek a cement anyagába, a távozó por pedig gyakorlatilag csak meszet és agyagot tartalmaz, amelyek a talaj természetes alkotói. A dioxinkibocsátás a kimutathatósági határ alatt van, a kén-dioxidot a mészkő megköti, és a folyamat végén nem képződik veszélyes hulladék.
***
A szerkesztő megjegyzései:
A gumiabroncshulladék anyagában való hasznosításának nagy lehetőségei lennének (útépítés, térburkolatok, stb.), amennyiben beruházási támogatást kaphatnának az erre vállalkozók. Ismeretesek alacsony hőmérsékleten működő szétválasztási technikák is, amelyek ugyancsak értékes nyersanyagot szolgáltatnak. A pirolízises hasznosításra is kész több vállakozó csoport, de nem jutnak beruházás közelébe, pedig szénhidrogén származékokat tudnának előállítani. A cementgyári égetés előtt ezeket a potenciálokat kellene kihasználni.
A cementgyárak nem önzetlenül és nem feltétlenül környezetvédelmi megfontolásokból égetnek gumit: szerte Európában sokat bírált tény, hogy olcsó és támogatott fűtőanyagra tesznek így szert. Először gumiabroncsot égetnek, aztán jobb sorsra érdemes műanyagot, aztán egyre veszélyesebb hulladékokat.
Tény, hogy évtizedes természetvédelmi vita után a Szársomlyó hegyet a felszínen nem bontja tovább a beremendi gyár, de a mélységi bányászat keményen folyik tovább. A Beremendi rög bányája, bár védett területet nem érint, komoly hatással van a szőlőhegyre és a karsztvizekre, károsíthatja a barlangrendszert.